2022 Sustainability Report | The Power of Science & Sustainability
Better science to solve the world’s toughest preservation challenges
2022 Sustainability Report The power of science & sustainability Be琀琀er science to solve the world’s toughest preservation challenges
Sustainability We live in uncertain times, facing an unprecedented combination of economic, social and geopolitical challenges. ese are also times that offer incredible opportunities for companies with the courage, vision and determination to seek meaningful change. Marc Doyle, CEO Dear stakeholders, We live in uncertain times, facing an unprecedented combination of economic, social and geopolitical challenges. These are also times that oer incredible opportunities for companies with the courage, vision and determination to seek meaningful change. Driven by our purpose of using beer science to solve the world’s toughest preservation challenges, Arxada is targeting such change in three key areas: protecting and maintaining the health and wellbeing of people, extending the life of vital infrastructure and improving the health of our planet. In our first sustainability report as a standalone company, we are proud to report on our progress in 2022. This includes establishing our sustainability team, designing our strategy and framework, and seing bold and ambitious goals, with the aim of embedding sustainability into everything we do across our three pillars of Planet, Preservation and People. We have demonstrated our proactive focus on sustainability from day one as a company. Thanks to support from our owners, Bain Capital and Cinven, the carve-out of Arxada was partially financed through Sustainability-Linked Financial Instruments, a first of its kind for a private equity transaction. This commitment to reducing our environmental impact during our early growth stage was just the beginning. We have subsequently made several notable sustainable investments and sharpened our sustainability strategy. The aim is to help our customers adapt to long-term environmental and social change and develop more sustainable solutions while we actively decrease our environmental footprint. Planet In 2022, we completed our inventory of all Scope 1, Scope 2 and Scope 3 emissions. We also submied our science- based targets to the Science-Based Targets initiative (SBTi) for validation in 2023, establishing a net zero goal by 2050. Moreover, we are leveraging our manufacturing process technology expertise to deliver more ecient manufacturing processes for some of our key chemistries, focusing on lower carbon dioxide (CO ) and greenhouse gas 2 (GHG) emissions.
Preservation We are helping drive the preservation industry’s transition to more sustainable and cleaner solutions through our partnerships and investments in boosters, potentiators and controlled release technologies. We continue to develop and launch innovative technologies and products that address our customers’ toughest challenges, meet increased regulatory pressures and improve the wellbeing of society. People We are working to create a culture of inclusivity for all through modern programs, benefits and structures that not only support employees to thrive and grow but enable Arxada and its people to have a positive impact in the communities where they work and live. Thank you for your interest in our sustainability journey. Marc Doyle, CEO
Our business & sustainability Arxada is a global specialty chemicals company, headquartered in Switzerland that was created in 2021 following the carve-out and sale of Lonza Specialty Ingredients to private equity firms Bain Capital and Cinven. With a long-standing history as a global leader in specialty chemicals, Arxada develops and manufactures a broad range of innovative products that address the growing need for more sustainable protection of human health and wellbeing, infrastructure and our planet. By doing so, the company aims to solve the world’s toughest preservation challenges. Our business, purpose & values Arxada focuses on four core end-markets: Human Health and Nutrition, Home and Personal Care, Paints and Coatings and Wood Protection, and provides a broad porolio of dierentiated products and solutions. This is supported by science and innovation capabilities, in-depth regulatory know-how and a proven record in manufacturing and process development. Arxada has a global footprint spanning 26 production sites and 16 research and development centers; we have a world-leading team of 3,600 employees, serving customers across a wide range of industries. We innovate to solve, challenge and remove barriers to peak performance. We are passionate about empowering high performance and realizing potential both internally and for our partners and customers. We work together every day to achieve our purpose: Better science to solve the world’s toughest preservation challenges 3,600 26 16 Employees Production R&D centers sites
Operating locations HQ and main Manufacturing sites Research and commercial sites development centers Auckland (New Zealand) Alpharea (GA, US) Global HQ Conley (GA, US) Bangkok (Thailand) Basel (Switzerland) Helena (AR, US) Blackley (UK) Horhausen (Germany) Castleford (UK) Huddersfield (UK) Conley (GA, US) Main commercial sites Kabinburi (Thailand) Florham Park (NJ, US) Bangkok (Thailand) Kalama (WA, US) Hannover (Germany) Del (Netherlands) Kourim (Czech Republic) Kourim (Czech Republic) Florham Park (NJ, US) Lake Charles (LA, US) Melbourne (Australia) Shanghai (China) Levelland (TX, US) Modesto (CA, US) Tokyo (Japan) Mapleton (IL, US) Morristown (NJ, US) Modesto (CA, US) New Plymouth (New Zealand) Moerdijk (Netherlands) Salto (Brazil) Nanjing (China) Shanghai (China) New Plymouth (New Zealand) Tokyo (Japan) Newark (NJ, US) Visp (Switzerland) Penang (Malaysia) Phoenix (AZ, US) Port Shepstone (South Africa) Rochester (NY, US) Salto (Brazil) Suzhou (China) Trentham (Australia) Valparaiso (IN, US) Williamsport (PA, US) Visp (Switzerland)
Our purpose centers around the importance of preservation for society and the environment. Preservation can protect and maintain the health and wellbeing of people, improve the longevity and ecacy of vital infrastructure, while supporting the health of our planet. To help us achieve our purpose, we follow a set of core values that reflect the longstanding commitments of our heritage companies, demonstrate our steadfast commitment to our people and the planet, and exemplify the way we work. These values are timeless and form the foundation of everything we do. Safety & Ethical Respect for health behavior people & planet Commiing to safety and We behave as respected health is a top priority for all of corporate citizens, in We treat all people with us. This encompasses our accordance with the highest professionalism, dignity and employees, our contractors, ethical standards and in respect, fostering an our customers and the people compliance with all applicable environment of collaboration, in the communities where we regulations and laws. innovation, excellence and do business. inclusion. We provide science- led solutions for our customers helping them to adapt to long- term environmental and social change and develop more sustainable solutions while we actively reduce our environmental footprint. Our products Preservation is about protecting and maintaining the health and wellbeing of people and improving the longevity and ecacy of vital infrastructure, while supporting the health of our planet. Our broad porolio of products and services helps our customers to be more ecient, eective and sustainable. Consumer Microbial Industrial Microbial Nutrition, Care & Control Control Environmental Professional Hygiene Vitamin Ingredients People Home & Personal Care Wood Protection Paints & Coating Composite Materials Infrastructure Material Protection
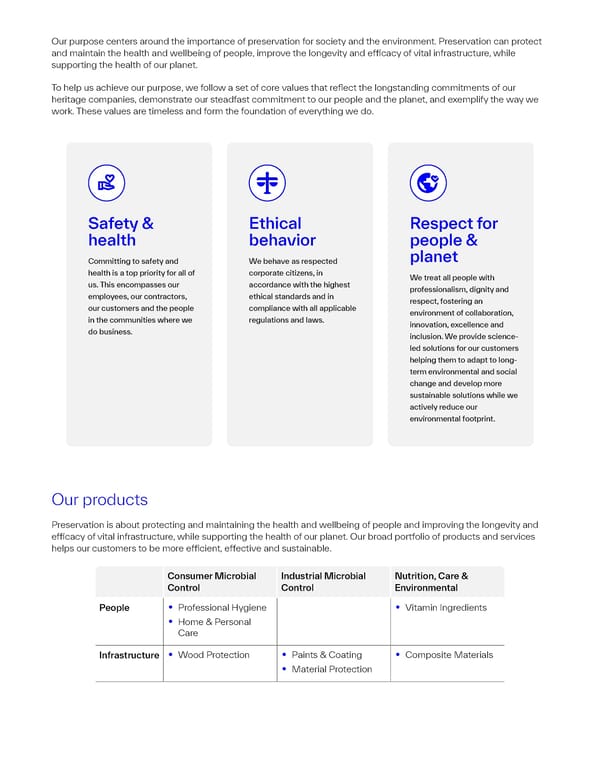
Consumer Microbial Industrial Microbial Nutrition, Care & Control Control Environmental Crop Protection Energy Custom Development Planet & Manufacturing Water Treatment Organization (CDMO) Developing our sustainability strategy In 2022, our first full year of operations as Arxada, we set the ambition of formalizing a sustainability strategy that can help us ensure we deliver on our purpose in a way that supports the UN Sustainable Development Goals (SDGs). Through our products, we want to subscribe to more sustainable solutions for the world’s toughest preservation challenges. Within our operations, we want to ensure that we are contributing to a low-carbon specialty chemicals industry and are creating healthy and safe environments for our employees. Our sustainability strategy enables us to do this by combining forward-thinking ambitions for our products with targets to reduce the environmental and social impact of our operations. In 2022, as part of our strategy development process, we conducted in-depth desktop research and engaged internal and external stakeholders across the globe through a series of interactive workshops and meetings. In addition, we engaged employees and investors, conducting a global customer survey to help inform and guide our strategy and priorities. The inputs from our research and stakeholder engagements were instrumental in identifying and prioritizing the sustainability issues most important to our business and our key stakeholders. The outcome of this work is refinement and focus on key issues that will drive our sustainability performance forward. We evaluated and synthesized our engagement findings, additional industry research and know-how from senior colleagues to develop a sustainability strategy for 2030, resting on the three pillars of Planet, Preservation and People. Going forward as a best practice, we will routinely seek input from all stakeholders and continue updating and refining our sustainability approach to reflect stakeholder priorities. Arxada’s sustainability strategy Planet Preservation People Operating eco-eciently and Protecting and maintaining the Caring for people and with respect for natural health and wellbeing of communities, creating healthy resources on our path towards people, improving the inclusive and safe workplaces net zero longevity and ecacy of vital where everyone can thrive and infrastructure while supporting grow the health of our planet
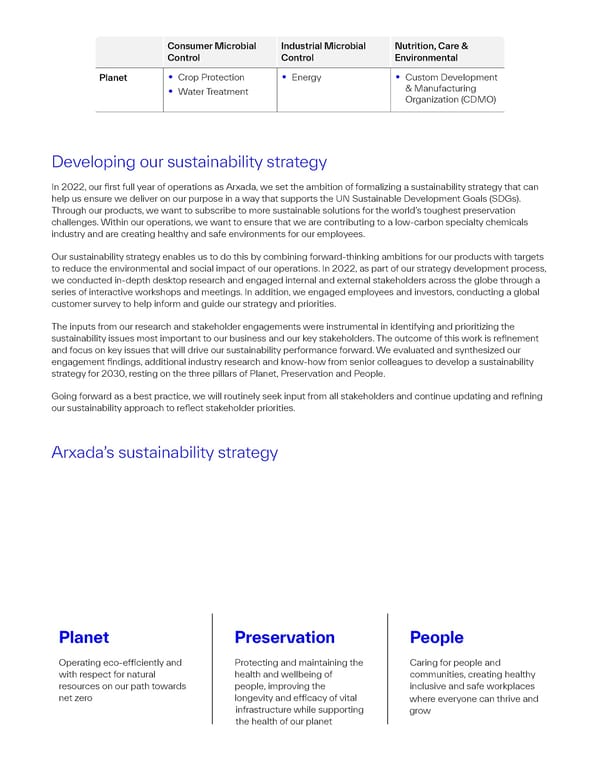
Net zero by 2050 Advancing the UN SDGs Towards world-class health through sustainable and safety throughout our Reducing our Scope 1, 2, and 3 preservation operations emissions to zero or to a residual level and neutralizing Our 2023 goal is to launch Achieve by 2030: [1] any residual emissions Porolio Sustainability TRIR (Total Recordable Assessments and set a goal for Injury Rate) < 0.3 sustainable solutions by [2] revenue for 2030 LTIFR (Lost Time Injury [5] Frequency Rate) < 0.1 50% reduction of scope 1 and Advocacy leadership for Creating an inclusive culture [1] 2 emissions by 2030 science-based decision- where all employees thrive making for a sustainable and grow As we are already ahead of our future 2030 goal, we will revisit and Increase female representation reset our 2030 goal in 2023 Collaborate, drive and sponsor in senior leadership to 40% by [6] >50 scientific advocacy events 2030 [3] by 2030 Water Responsible sourcing: Community engagement and addressing sustainability in positive impact through Goal to be set in 2023 our supply chain volunteering 100% of key suppliers to Employees share or contribute complete an ESG assessment 46,000 volunteer hours by [4] by 2030 2030 [1] From our 2021 baseline. [2] As per the WBSCD PSA or another 3rd party validated methodology. [3] Rates are calculated as the number of injuries or incidents in the reporting period x 200,000 / Total hours worked in the reporting period. [4] Our key suppliers make up approximately 20% of our supplier base and account for approximately 80% of our spend. [5] Advocacy to advance external science-based decision making that drives sustainable preservation. [6] Our senior leadership includes the following job roles: Associate Director; Director; Senior Director; Vice President; Senior Vice President; President; and CEO. Sustainability-Linked Financial Instruments In a first of its kind for a private equity transaction, the carve-out of Arxada was partially financed through sustainability-linked loan facilities and sustainability-linked bonds (Sustainability-Linked Financial Instruments), with support from our sponsors Bain Capital and Cinven. A Sustainability-Linked Financial Instrument has financial and/or structural characteristics that can vary depending on whether the issuer achieves material, ambitious, pre-determined, regularly monitored and externally verified sustainability objectives. Therefore, Sustainability-Linked Financial Instruments present an additional incentive for the issuer to meet future commitments to improve sustainability in areas considered material to overall business operations. This is particularly relevant for Arxada as by embedding targets against its Key Performance Indicators (KPIs) into Sustainability-Linked Financial Instruments, Arxada has commied to reducing its environmental impact during its early growth stage. Arxada is also ensuring continuous and transparent disclosure of performance on these KPIs, as the company develops.
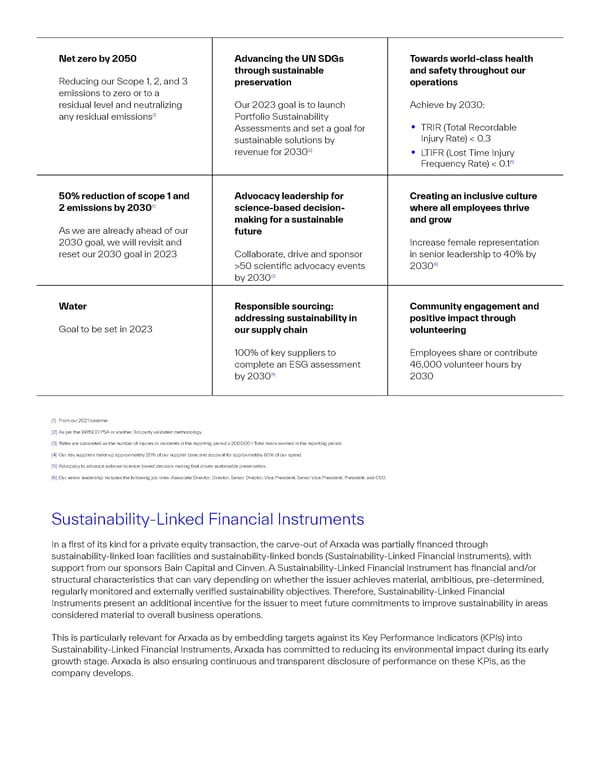
The adopted KPIs tied to the Sustainability-Linked Financial Instruments are (i) our greenhouse gas (‘‘GHG’’) emissions intensity and (ii) waste intensity with target reductions set from a 2018 baseline. By intensely focusing our resources to meet the reduction goals, as of the first interim target date of 2022, we have exceeded the goals set on both targets. A Sustainability-Linked Financing Report will be provided to Investors by Arxada on the progress made against the KPIs of each Sustainability-Linked Financing Instrument. External verification of our assessment of performance against the KPIs of each Sustainability-Linked Financing Instrument will be conducted on at least an annual basis beginning the fiscal year end 2022. See our assurance statement for our 2022 KPI observation data here. More information on how we are working to improve our GHG and waste impact and meet our targets can be found in the Planet Pillar content.
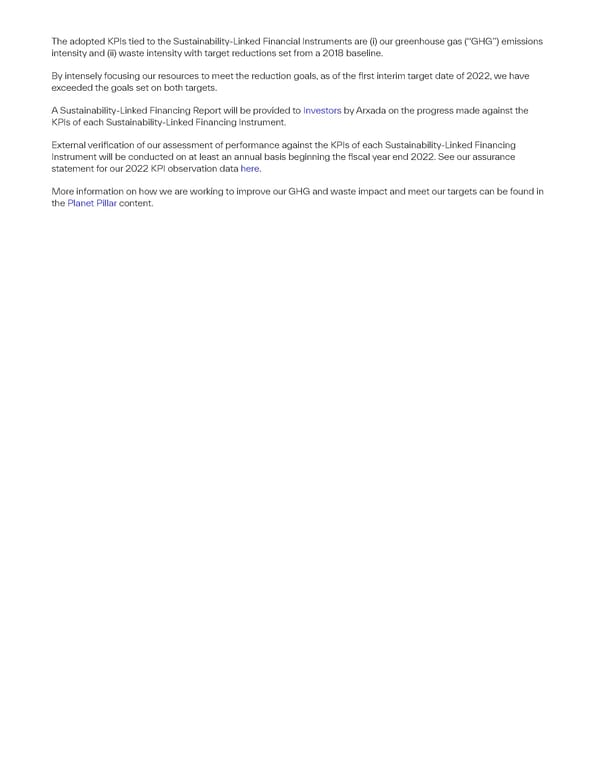
Sustainability governance Good corporate governance is important for the success of our business. In 2022, we formalized the governance structure for the successful delivery of our sustainability strategy. This included oversight and due diligence at the highest level of the business, establishing the right policies and mechanisms to guide ethical business practices and ensuring adherence to recognized sustainability frameworks and certifications. Our 2022 site certifications and publicly available policies supporting our sustainability eorts are available on our Resources & downloads page. Our board & ELT sustainability responsibility Our board of directors is responsible for overseeing Arxada’s strategy, risk management and corporate reporting. The board is comprised of ten members, including three independent members (two of whom joined our board in January 2022), four members from Bain Capital and three from Cinven. The board does not include members of our Executive Leadership Team (ELT) responsible for the daily management of our business. Forming part of our wider governance and reporting to the board, we have three commiees in place: an audit commiee, a people commiee and a sustainability commiee. In 2022, the sustainability commiee focused on developing our sustainability strategy and associated targets; in 2023, the focus will be on the strategy’s institutionalization and execution. To support our sustainability commiee and progress on our sustainability strategy, we also have a two-person sustainability team which reports to our Chief Technology and Sustainability Ocer. Demonstrating our commitment to driving positive impact, we linked the remuneration of our ELT members to our safety performance. As we were still defining our sustainability strategy in 2022, we included Arxada’s safety performance as part of our short-term incentive program. With our strategy now finalized, in 2023 we will consider how to further integrate sustainability-related metrics into our remuneration and incentive program. Board of directors Our board of directors consists of ten members and is responsible for overseeing Arxada’s strategy, risk management and corporate reporting. The board is also responsible for approving our overall sustainability strategy.
Sustainability commiee Composed of eight members, including our Chief Executive Ocer (CEO) and Chief Technology and Sustainability Ocer and four representatives from Bain Capital and Cinven, the sustainability commiee is responsible for the measurement, improvement, and reporting of our environmental and employee safety impact plans, and works to develop and execute plans for our environmentally [1] [2] related remedial actions for existing sites. The sustainability commiee also works closely with other members of our business to ensure sustainability data is thoroughly understood and reported, and that sustainability topics are eectively communicated and managed throughout the organization. Audit commiee Composed of three members from Bain Capital and Cinven, with participants including our CEO and Chief Financial Ocer, our audit commiee assists the board with its oversight responsibilities to the members, potential members, the investment community and others (as appropriate) relating to (i) the integrity of the Company’s financial statements; (ii) the eectiveness of the Company’s internal control over financial reporting; (iii) selection of the independent auditor and assessment of the independent auditor’s qualifications and independence; (iv) the performance of the Company’s internal audit functionality and independent auditors; and (v) the performance of the other commiee functions. People commiee Composed of seven members, including our CEO and Chief People Ocer, and four representatives from Bain Capital and Cinven, our people commiee is responsible for providing strategic input to advance a transformational people agenda focusing on building a strong employer brand. Executive Leadership Team Our ten-person ELT is responsible for managing our day-to-day business and defining our overall strategy, including our purpose, vision, and sustainability strategy. Sustainability team The two-person sustainability team reports to our Chief Technology and Sustainability Ocer. They play a key role in facilitating ongoing communication and driving the implementation of our sustainability strategy. [1] GHG, waste and water. [2] Total Recordable Injury Rate and Lost Time Injury Frequency Rate. Business ethics Our policies form the foundation of our ethical business conduct by seing standards for our employees and suppliers, who are expected to adhere to our policies and act with integrity. The foundations of our principles and values for ethical behavior are set out in our Code of Conduct. In 2022 we introduced several new ethics and compliance policies, including a Code of Conduct, Anti-Bribery Policy, Business Gi Policy, Antitrust Policy and Whistleblower and Non-Retaliation Policy. We initiated a new compliance program that requires our employees to undergo an annual training on the Code of Conduct. They will also be trained in
two to three rotating topics. We have customized our training programs, ensuring that employees receive content that is relevant and thorough. Training provided in 2022 included Code of Conduct, Anti-Bribery and Conflicts of Interest. In 2023, we are training on Antitrust, Harassment, Confidential Information and Computer Security. Expanding on our global training and policies, we will provide training that is targeted and region-specific. This may be based on potential compliance risks identified for a region or the need to adhere to specific local laws and regulations. For example, we created and implemented region-specific policies for our Chinese sites that are available in the local language. We regularly communicate the importance of compliance and business ethics through training, wrien materials and our Arxada intranet. All employees have access to our whistleblower program, which includes a hotline and an online portal. The program is available 24/7, in all our operating languages, to allow employees to flag compliance issues they may observe. Employees who raise concerns and compliance issues are protected through our Whistleblower and Non-Retaliation Policy, ensuring anonymity. HIGHLIGHT Navigating business in a complex & interconnected world We have suspended all business operations in Russia since 1 April 2022. Our business in Russia represented an exceedingly small proportion of our operations, consisting of four employees working in our sales group. We have no manufacturing facilities in either Russia or Ukraine, nor do we receive any strategic raw materials from these countries. So far, the conflict has had only an extremely limited business impact on markets outside this region. As part of the global humanitarian eort that has been mobilized in response to the crisis, Arxada donated USD 100,000 to the International Medical Corps — an independent, not-for-profit organization that operates worldwide to provide emergency relief and long-term support to those aected by war, disaster and disease.
About the 2022 sustainability report Herens Midco S.à r.l. is a private limited liability company incorporated under the laws of Luxembourg on January 28, 2021. Arxada AG and Troy Corporation are indirect subsidiaries of Herens Midco S.à r.l. and operate under the name Arxada. Arxada’s operational headquarters is in Basel, Switzerland. This inaugural annual sustainability report, available for download on arxada.com, covers the activities of the Group from January 1, 2022, through December 31, 2022, unless otherwise noted. To determine the KPIs and disclosures in this report, we referenced the Global Reporting Initiative (GRI) Standards (2021) and the Sustainability Accounting Standards Board (SASB) Resource Transformation - Chemicals (RT-CH) Standard. This report and the data included is intended to help our stakeholders understand our sustainability performance. Sustainability performance data on GHG intensity and waste intensity for our sustainability-linked loan requirements have been assured by an external third party. Arxada is commied to increasing the scope of our sustainability data collection and data assurance in future years. For questions, comments, and suggestions about our report or this website, please email us at [email protected]. For investor inquiries about our sustainability practices please email us at [email protected]. For media enquiries please email us at [email protected]. Forward-looking statements This annual report contains forward-looking statements. Forward-looking statements provide our current expectations, intentions, or forecasts of future events. Forward-looking statements include statements about expectations, beliefs, plans, objectives, intentions, assumptions and other statements that are not statements of historical fact. Words or phrases, or the negatives of those words or phrases, may identify forward-looking statements. Still, the absence of these words does not necessarily mean that a statement is not forward-looking. Forward-looking statements are subject to known and unknown risks, uncertainties and other factors. They are based on potentially inaccurate assumptions that could cause actual results to dier materially from those expected or implied by the forward-looking statements. Given these risks and uncertainties, you should not rely on forward-looking statements as a prediction of actual results. We urge you to read this entire annual report, including the sections on factors that could aect our future performance and the industry in which we operate. Any forward-looking statements are only made as of the date of this annual report. We do not intend nor assume any obligation to update forward-looking statements set out in this report. You should interpret all subsequent wrien or oral forward-looking statements aributable to us or to persons acting on our behalf as being qualified by the cautionary statements in this annual report. As a result, you should not place undue reliance on these forward-looking statements.
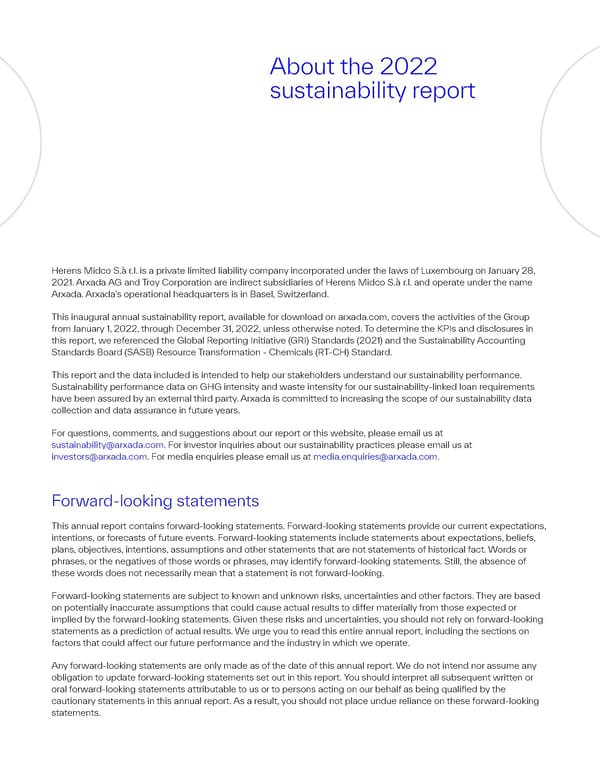
Planet As we come to realize our responsibility for environmental stewardship, we see a magnificent opportunity for innovation focusing on the environmental impact of everything we do. is journey will ultimately result in preserving our environment and achieving net zero. Mike Burness, Head of Global Quality and Sustainability Our environmental eorts are focused on operating eco-eciently and respecting the planet’s natural resources on our path toward net zero. This includes working to reduce our greenhouse gas (GHG) emissions, as well as improving our water and waste management. In 2022, our first full year operating as Arxada, we have worked to align the management of our environmental topics across our global operations network. To ensure a continued and globally aligned approach, we have set three global priorities that our business will work towards over the coming years. Please read more about the current and future management of our environmental topics and progress made in 2022 on the following pages.
Goals NET 50% Water Reduction of Scope 1 Goal to be set in ZERO and 2 emissions by 2023 [1] By 2050 2030 Reducing our Scope 1, 2, and 3 As we are already ahead of our emissions to zero or to a residual 2030 goal, we will revisit and level and neutralizing any residual reset our 2030 goal in 2023. emissions [1] From our 2021 baseline.
Air quality & GHG emissions To help preserve our planet and limit global warming, reducing the emissions of greenhouse gases (GHG) and other air pollutants is a key priority for Arxada. While we believe our products can have an enormous positive impact, we are looking to improve the eciency of our facilities and supply chain, contributing towards a reduction in our environmental footprint. Our ambition is to become a low-carbon chemicals company with a net zero carbon footprint. GHG intensity reduction targets were integrated into the Sustainability-Linked Financial Instruments issued as part of our carve-out as Arxada. In 2022, we went even further by submiing science-based targets to be validated by the Science Based Targets initiative (SBTi), establishing the following goals: NET ZERO 50% [1] By 2050 Reduction of Scope 1 and 2 [1] emissions by 2030 Reducing our Scope 1, 2, and 3 emissions to zero or to a residual level and neutralizing any As we are already ahead of our 2030 goal, residual emissions. we will revisit and reset our 2030 goal in 2023. [1] From our 2021 baseline. Our Scope 1 & 2 emissions In 2022, we completed a GHG inventory for our Scope 1 and 2 emissions. Scope 1, which is responsible for most of our combined Scope 1 and 2 emissions, includes emissions from fuel combustion, as well as natural gas and refrigerants used in our manufacturing processes and facilities. Scope 2 is a smaller portion of our emissions and is split between the electricity and steam used in our manufacturing processes and facilities. As we are already ahead of our 2030 goal, we will revisit and reset our 2030 goal in 2023.
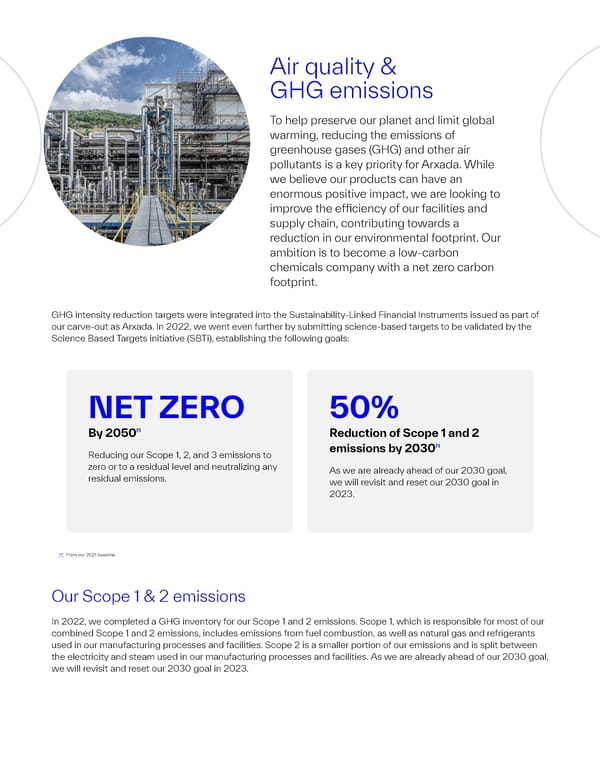
To meet our net zero by 2050 target, we will be working to reduce our emissions in line with our SBTi submied targets. We continue to analyze various emission sources for reduction opportunities across our facilities globally. At the end of 2021, the installation of a catalytic converter in Visp, our largest production site, led to a significant reduction in nitrous oxide (N O), which forms a significant portion of our global Scope 1 emissions. In its first year of use, the 2 converter has allowed us to reduce our N O emissions in Visp by over 98%, the equivalent of 520,000 tCO e. Find out 2 2 more about the catalytic converter project in the case study. Reducing our Scope 2 footprint, which is driven by our purchased steam and electricity, is another priority. These energy sources are used to run our daily operations. Throughout the business, we are seing reduction targets and building decarbonization and sustainability plans. As a result, we are working to identify opportunities to replace equipment with newer and more ecient models. This is particularly impacul as we are seeking to increase the use of renewable energy across the business. Scope 1 & 2 distribution Scope 1 Scope 2 (market-based) Our Scope 3 emissions As part of our SBTi target submission in 2022, we evaluated our Scope 3 footprint from 2021, which makes up nearly two-thirds of our GHG emissions. Upon validation of our SBTi targets, we will set specific Scope 3 goals. The largest category of our Scope 3 emissions is purchased goods and services which includes raw materials used in production. Alongside eorts to reduce our consumption of raw materials, we work to advance responsible sourcing and waste management eorts, thus helping to reduce our Scope 3 footprint. Examining our Scope 3 footprint in more detail, we have identified raw materials with the most significant impacts on our emissions by examining their GHG intensity. One of our approaches to reduce our Scope 3 emissions is to explore the feasibility of recovering, recycling and reusing raw materials. In 2023, we will continue to work to beer understand our Scope 3 footprint and reduce our emissions, focusing on our raw materials. Air pollutants In addition to the commonly reported GHG emissions, Arxada regularly monitors our emissions for sulfur oxides (SO), x nitrogen oxides (NO) and volatile organic compounds (VOCs). We ensure these emissions are regularly measured and x reported to local authorities in line with the regulations of the various operating regions.
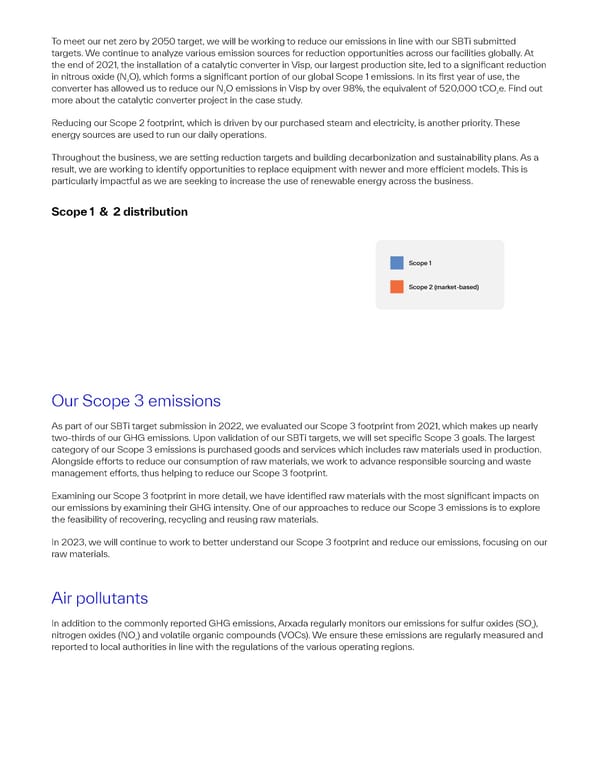
Arxada’s air pollutants VOCs NO x SO x Looking forward to 2023 In 2023, we will formalize our science-based targets, continue to advance our emission reduction initiatives and work to identify additional opportunities to decrease our footprint. To support our goal of reducing emissions, we will develop decarbonization plans throughout the company. We will continue to monitor, track and examine our energy consumption and look to increase eciency and use of renewable energy. This is important as we consider ways to electrify processes that currently rely on natural gas. We will closely analyze our raw material usage, supply chain and waste management to identify chances to reduce our Scope 3 emissions. HIGHLIGHT NO reduction in Visp, Switzerland 2 In 2019, we detected that as part of our Vitamin B3 production process at our Visp (Switzerland) manufacturing facility, we emied N O. While nitrous oxide does not present a risk to health, it is a potent GHG contributing to our 2 Scope 1 emissions. We saw an opportunity to improve our process eciency and environmental impact.
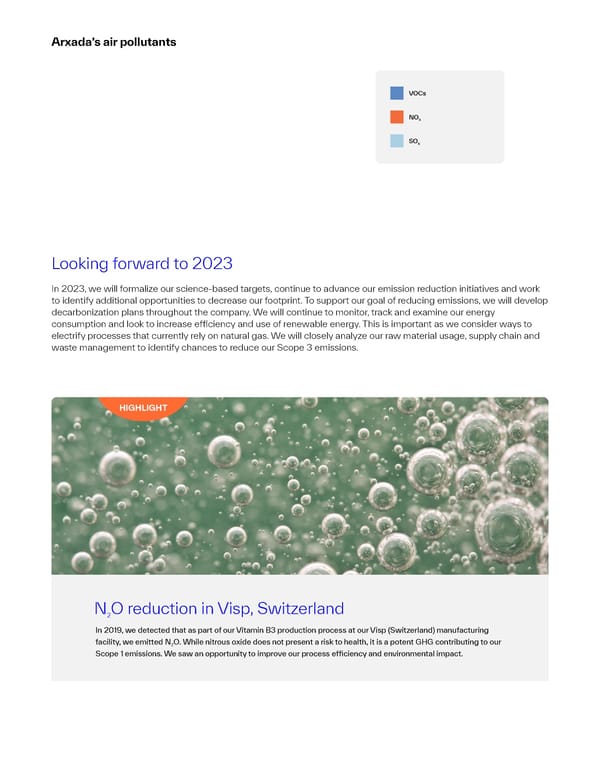
Following a detailed investigation into the production process and a feasibility study, including the localization of technology to help us reduce our N O emissions, we installed a new catalytic converter at our facility and began 2 operating it in October 2021. The converter decomposes the N O into N and O which can be released into the 2 2 2, atmosphere without concern. Aer the converter’s installation, measurements showed that the conversion of N O 2 were carried out to almost 100%. In 2022, its first full year of operation, the converter allowed us to reduce approximately 1,750 tons of N O 2 emissions, the equivalent of 520,000 tCO e. This has led to a reduction of more than 70% of our global Scope 1 2 emissions.
Waste management Waste is a by-product of many manufacturing processes, including ours. Managing dierent waste streams and finding ways to reduce it is a large part of our process optimization and key for protecting our planet. Local communities have a vested interest in wanting to be reassured about proper waste disposal. We recognize the broader role we play in reducing our environmental impact and conserving natural resources to support a more circular economy. Responsible waste management and decreased waste generation is an important component to our environmental objectives. Our waste minimization guidelines prioritize best practices and clarify responsibilities for sites to manage and reduce waste. Additionally, it is important for us to take a site-specific approach to waste reduction, as waste classification and regulatory requirements vary by location and must be localized to ensure compliance. Reducing our waste has many direct and indirect benefits, such as increasing material eciency, diminishing raw material purchases and reducing our Scope 3 footprint. In Visp, for example, a waste reduction project led to a smaller amount of waste treated externally through a high-intensity energy treatment, thus avoiding emissions and reducing our water consumption. Our waste minimization plan We are building waste management plans throughout the company. We use a centralized global data system and process to capture and manage environmental data from our manufacturing sites. This data reviews the links between activities, materials, products, supplies used and the waste generated. We then apply Arxada’s prioritization scheme that considers regulatory requirements, risk reduction, and environmental benefit (amongst other factors). Once suitable waste streams for reduction have been identified, our sites turn to our waste minimization hierarchy to identify and achieve sustainable waste reduction. Arxada 2022 Sustainability Report
Prevent Reduce Reuse Preventing waste from being Reducing the quantity of waste Using a product, material, or produced being produced substance again for the same purpose [1] Recycle Energy Disposal recovery Recovering waste and Directing waste towards reprocessing it into products, landfilling and other final solutions Converting waste materials into materials, or substances usable heat, electricity, or fuel [1] Recycling includes composting but does not include incineration. To ensure our waste management is aligned with regional regulation and industry best practices, while considering newly available technological solutions, our site teams periodically review the performance of waste management practices to implement updates and changes. Waste data is collected quarterly and reported annually through this report. Waste management in action The classification of waste as hazardous or non-hazardous at our facilities depends on the applicable regional regulations. We frequently look to implement industry best practices to minimize our total waste footprint and turn hazardous waste into non-hazardous waste. Arxada’s waste footprint 75,000 t Hazardous waste 60,000 t Non-hazardous waste 45,000 t 30,000 t 15,000 t 0 2021 2022 In 2022, as part of our ongoing process optimization work, we discovered some of the hazardous waste we produced in Visp (Switzerland) can be sent to an external waste treatment plant for further purification. By using separation technologies like distillation, we can extract some of the oen expensive and GHG intense solvents from the waste to recycle and reuse in our processes. This allows us to keep materials in the system longer, reducing raw material purchasing costs, reducing our carbon footprint and supporting circularity in our processes. Equally, the separation Arxada 2022 Sustainability Report
technology allows us to extract water from the waste, which is sent to a treatment plant and released back into the local water body. We now send significantly less material to the external waste treatment plant, allowing us to reduce our hazardous waste in Visp by 13,900 t and reduce water consumption. Looking forward to 2023 To continue driving sustainable waste reduction in 2023 and beyond, all our sites will work to develop waste reduction plans following our guidelines on waste minimization. Where further prevention and reduction of waste is not possible, we will continue our path towards circularity, as we look to explore alternatives for the by-products created in our processes. This includes reusing them in our own operations or selling them to other companies who use these materials in their processes. Equally, we will continue to reuse and recycle materials where possible, minimizing resource consumption and working towards a more circular way of operating. HIGHLIGHT Implementing safe working conditions in new sites As part of our merger with Troy Corporation in 2021, we added a manufacturing facility in Newark (NJ, USA) to our site porolio. Following an evaluation of the site, we established that almost 2,000 containers of material were congesting the operational flow and impacting its safe operation. In 2022, we extracted approximately 2,500 pallets of material from the site. This has allowed us to create more onsite storage space and safer working conditions for our employees. They can now pass through the facilities without obstruction, allowing the safe passage of forklis and individuals through the facilities. This is particularly important as there is a potential for flooding, which could cause additional health and safety concerns in the event of improperly stored and secured material. For 2023, we plan to remove the remaining 500 pallets of material from the site.
HIGHLIGHT Implementing wastewater treatment to improve eciency & reduce costs In 2022, our facility based in Rochester (NY, USA) began working to implement manufacturing process upgrades for ongoing compliance with wastewater regulations for the local county’s pre-treatment facilities. In 2019, the New York State Department of Environmental Conservation (NYSDEC) announced a new limit for wastewater discharge. Since then, we have been working with the state and county to ensure our Rochester site's safe and lawful operation. In 2023, to adhere to the new limit, we are rolling out a program that allows us to improve the monitoring of key wastewater parameters, reduce the generation of hazardous waste and streamline operational tasks. To reduce the generation of hazardous waste, we are installing new equipment that acts as a waste concentrator, allowing us to extract organics from our wastewater. This reduces the process’ hazardous waste by 115 metric tons annually and recycles the water back into the process. Additionally, by installing a new online analyzer for process control, we will be able to reduce organics in wastewater, improve the yield of our process, and reduce the use of materials in order to decrease our annual material costs.
Water management An essential resource for our operations, water is used in a variety of ways across our facilities: we use water not only to cool our processes and to produce steam, but also to mix with other materials, such as solvents, as part of our manufacturing processes. Carefully managing our consumption is a priority for us in an increasingly water scarce world. Considering our diverse use cases for water, in 2022, we determined that we needed to update our water data collection approach and further embed our data collection processes into the operations. While we are continuously working to reduce our water consumption, we will set water reduction targets in 2023. Similar to our waste management approach, local site management is responsible for water use and discharge, as well as collecting accurate data for our global data management system. Water withdrawal, use & release We typically draw water from our own groundwater wells, or nearby rivers and lakes, when available. Otherwise, we rely on water supplied by municipalities. Aer we withdraw water, we use it for various purposes within our facilities: . To cool down our processes . To produce steam . For cleaning processes . To combine it with our raw material to generate our products . For sanitary purposes within our facilities We use and dispose of water in ways that respect and adhere to the local requirements, regulations and industry best practices. This includes releasing water back into water bodies or municipal water streams, discharging it into wastewater treatment plants. Cooling water in Visp Visp in Switzerland, our largest production site, is located near the river Rhône. Due to its close proximity to the Swiss Alps, the river is naturally cold, holding a temperature between approximately 4°C–8°C year-round. This natural source of cooling water allows us to operate our facilities in Visp without energy-intensive cooling towers. To ensure we are respecting and optimizing the use of this natural resource, we are currently conducting an analysis to determine our use eciency. Aer identifying potential areas for optimization, we seek to actively lessen use by implementing a closed-meshed monitoring concept. With deeper understanding, we will start developing strategies to maximize reduced consumption.
Looking forward to 2023 In 2023, we will set water reduction targets companywide and will work closely with our manufacturing sites to preserve this important and critical resource. HIGHLIGHT Stormwater collection & water recycling in Auckland, New Zealand Our manufacturing facility in Auckland (New Zealand), uses water to produce our Tanalith C Oxide product. In 2022, we increased the amount of stormwater and recycled water to decrease our use of industrial water from the local town supply. Stormwater within our site is captured and led through an underground sand filtration system before being transferred to two storage tanks within our facility grounds. Equally, water used in our onsite laboratory and for washing up, for example, is captured and diverted to a wastewater tank to be recycled for use in our Tanalith C Oxide production process. While these systems have been in place for a few years, we increased our focus on using stormwater and recycled water in 2022, using in total, 581,509 liters with a record amount of 79,764 liters of stormwater in August 2022. Our stormwater and recycled water contributed 34% of our water needs for the Tanalith C Oxide production process, which is more than double the amount used only two years ago in 2020.
Preservation We are committed to being the industry leader in sustainable preservation — protecting and maintaining the health and wellbeing of people, and extending the life of vital infrastructure while working to reduce both our own and our customers’ ecological footprint. Rick Strimaer, Chief Technology and Sustainability Ocer Our vision is to tackle the most pressing preservation challenges for people and the planet, we recognise the crucial role that our products play in achieving this goal. Through our products and solutions, we are working to protect the health and wellbeing of people and improve the longevity of infrastructure and materials to preserve the health of our planet. We are dedicated to continuously upgrading the sustainability of our products throughout their lifecycle and developing newer, more environmentally friendly technologies in line with global regulatory requirements. This includes being mindful of the materials we use, how we source them and using science to advance sustainability. To achieve our goal of sustainable preservation, we have established three targets for 2030. Learn more about our targets and progress on the following pages.
Goals Protecting and maintaining the health and wellbeing of people, improving the longevity and ecacy of vital infrastructure while supporting the health of our planet. Advancing the UN Advocacy leadership Responsible SDGs through for science-based sourcing: addressing sustainable decision making for a sustainability in our preservation sustainable future supply chain Our 2023 goal is to Collaborate, drive and 100% of key suppliers launch Porolio sponsor >50 scientific to complete an ESG [3] Sustainability advocacy events by assessment by 2030 [2] Assessments and set a 2030 goal for sustainable solutions by revenue, [1] for 2030 [1] As per the World Business Council for Sustainable Development (WBSCD) Porolio Sustainability Assessment (PSA) or another 3rd party-validated methodology. [2] Advocacy to advance external science-based decision-making that drives sustainable preservation. [3] Our key suppliers make up approximately 20% of our supplier base and account for approximately 80% of our spend.
Advancing the UN SDGs through sustainable preservation At Arxada, we understand that preservation and sustainability go hand-in-hand. By increasing the longevity of something, whether it be a physical material or the health and wellbeing of people and the planet, we are helping to build a more sustainable future. Some of our products act directly as preservatives, through material protection. Other products work to combat harmful microorganisms and improve hygiene, helping to support healthier societies. To ensure we are aligned with the needs of society, we will begin the assessment of our product porolio in 2023 and set a sustainable solutions revenue goal for 2030. This will be evaluated using the World Business Council for Sustainable Development (WBCSD) Porolio Sustainability Assessment (PSA) or another 3rd party-validated methodology. Improving the impact of our products Our commitment to sustainability is closely tied to our focus on innovation and technology. Considering the recent pandemic, we recognize the critical importance of keeping people, places and the planet healthy. Our eorts to achieve sustainability encompass a range of initiatives, including preserving current technologies that protect public health and developing new, greener and more sustainable chemistries and products. One of our key areas of focus is preventing microbial contamination in consumer products. Such contamination can have significant financial and reputational implications for manufacturers and marketers. Our preservatives are designed to inhibit the growth of harmful bacteria, yeast and fungi, thereby extending the shelf life of personal care and cleaning products. As microbes continue to evolve due to increasing population density and climate change, the threat they pose to people, places and the planet are constantly evolving. We remain commied to staying at the forefront of technology and innovation to protect public health while promoting sustainability. We have created and instituted a product development process that goes beyond basic regulatory compliance and focuses on performance, environmental and safety goals for the benefit of customers, employees and end-users alike. In developing our products, our research and development (R&D) and operational teams work together to ensure our products support preservation in their end uses. For example, products that form a component in paints and coatings can be used to protect and preserve the material of the surface it is used on. Coatings used on wind turbines that produce renewable energy must withstand harsh weather conditions, while coatings used on appliances must withstand everyday use. Our teams work closely to ensure that our products meet all current and anticipated regulatory requirements.
In 2022, we conducted research to identify reliable and accepted approaches to evaluate and measure the impact of our products throughout the lifecycle and alignment with the United Nations Sustainable Development Goals (UN SDGs). In 2023, we will begin testing these methodologies on key products and new product innovations within each of our business units. This includes working with external frameworks, tools and experts, including the WBCSD PSA, and tools for Product Carbon Footprinting (PCF). Innovating sustainable products Arxada’s purpose is to advance beer science to solve the world’s toughest preservation challenges. Preservation is about protecting and maintaining the health and wellbeing of people and improving the longevity of vital infrastructure, while improving the health of the planet. Our ambition is to innovate and be part of eorts to address the UN SDGs. Eective preservation enhances the durability of water-based products which significantly reduces waste throughout global supply chains. Preservation solutions are essential to ensure minimization of waste and safety of products. Without eective preservation, not only will significant amounts of energy and natural resources go to waste, the development of sustainable products such as paints and coatings will also be limited. This has impacts on the UN SDGs including climate change (SDG 13) and responsible consumption and production (SDG 12). Around the globe eective preservation solutions are under threat due to increasing regulatory constraints. An increasing number of suitable active biocidal substances are cancelled, not supported, non-approved, or restricted for use. New innovative technologies are needed that make use of the currently eective biocidal actives combined with new delivery mechanisms and optimization of solutions. In addition, sustainable innovations such as bio-based technologies, adjuvants and potentiators will need to be developed. Innovations for microbial control will require major investment and a focused eort, with long timelines to success. Partnerships and coordination with customers, NGOs, and regulatory authorities are needed to reduce the uncertainty of the ever-changing regulatory requirements. Arxada will provide insight into the most exciting developments as a responsible innovation leader and showcase new technologies that push the boundaries of what is possible for achieving more sustainable preservation solutions. Looking forward to 2023 In 2023, we will begin deploying the WBCSD PSA to proactively identify and address improved sustainability outcomes of new product innovation, ranging from the product chemistry to the SDG impacts of our products. Implementing a common methodology built on industry best practices provides a robust, pragmatic and integrated approach to steer our product porolio sustainable innovation eorts. As sustainable design definitions and methodologies evolve, we will adapt to ensure we are holistic in our approach to sustainable innovation.
HIGHLIGHT Expanding our hygiene porolio using sustainable chemistry For several years, we have been working to expand our hygiene product porolio to include disinfectant cleaners based on sustainable chemistry. The eorts of our North American hygiene product team have led to the development and launch of several products that utilize active and inert ingredients included on the U.S. Environmental Protection Agency’s (EPA) Safer Choice Ingredient List (SCIL). We began by expanding our porolio with disinfectant wipes and liquids based on Hydrogen Peroxide, which ® breaks down into oxygen and water. These products include our NUGEN enhanced hydrogen peroxide (EHP), ready to use (RTU) wipes for industrial and institutional markets (I and I), and consumer applications, the former of which is also approved by the EPA’s Design for the Environment, a certification for pesticides administered by EPA’s Safer Choice Program. For our work, we earned a Safer Choice Partner of the Year award in 2021. ® This year, we continued expanding our sustainable product porolio through the launch of our NUGEN Citric Guard Disinfectant wipes (CG Wipes). We partnered with a substrate producer to develop the CG Wipes, enabling us to develop a wipe substrate based on cellulose fibers approved on the SCIL. While we are awaiting approval for EPA’s Design for Environment certification, the CG Wipes have already been approved for a United States Department of Agriculture (USDA) Bio Preferred certification that calculated a 94% biobased content of our wipes. The CG Wipes were developed for the North American market; it is undergoing registration with the U.S. EPA and Health Canada, and we are currently testing and exploring the regulatory requirements for other regions like Australia.
HIGHLIGHT ® Tanasote – helping keep wood in the game Industrial timber still has many applications in today’s world, including railway sleepers, utility poles, as well as in heavy-duty agricultural applications. Traditionally, Creosote (a wood preservative pesticide) has been used to protect the timber and increase its longevity. Notably, the safety and environmental credentials of Creosote have been under review in Europe for years, and its use has been restricted under the EU’s Biocidal Products Regulation (BPR). Over the past decade, our wood protection R&D team has worked to develop a BPR authorized alternative; in April ® 2021, we introduced Tanasote . The oil-based copper wood preservative is designed to deliver a long service life (typically beyond 40 years depending on timber species and end-use application), while minimizing the risk of early failures. It is the only oil-based wood preservative approved under the BPR, and all its active ingredients are ® approved for wood preservative use in Europe. Tanasote has passed the BPR’s risk assessments to be used for the treatment of timbers in industrial heavy-duty applications both above ground and in-ground contact. During our extensive R&D process, we tested the performance of the product beyond the required industry standards to ensure that a longer service life for industrial-use timber can be achieved. This included testing in high humidity, aggressive field test sites and laboratory fungal studies. In addition, to provide confidence in our test performance data, it was reviewed by a third party and we engaged in full scale trials with commercial partners across Europe, including railway sleepers, utility poles, equestrian and agricultural fencing.
Advocacy leadership for science‑based decision‑making for a sustainable future Evolving our approach and staying up to date with new regulations are essential to developing products that serve the needs of the planet, communities and our customers. Our long history in the specialty chemicals sector has allowed us to develop deep industry expertise and understanding of the global regulatory landscape. To continue providing industry leadership and supporting the use of good science to advance sustainability, we have a strong presence in national, regional and global industry associations. We maintain direct contact with decision makers, authorities and regulatory agencies. For 2030, we have set the target to collaborate with customers and industry and to drive and/or sponsor more than 50 events advancing scientific advocacy. To us, this means advocating to advance external science-based decision-making that drives sustainable preservation. Our global regulatory & advocacy approach The Arxada global regulatory and advocacy approach is aimed at providing leadership and stewardship to place compliant and sustainable products and services on the market, meet the needs of our customers and keep people and the environment safe. We are striving to enhance the value we provide to our customers. International experience, combined with knowledge of local markets and regulations, are essential in the changing global business climate. Regulatory and advocacy practices are one of the key dierentiating factors helping to achieve strategic and sustainability objectives, and we are commied to lead on these eorts. Our regulatory and advocacy strategy is supported by a team of over 70 regulatory aairs experts around the world, oering a global, yet market-specific approach. Some of the key organizations we engage with and are active members of include: ACC CBC ACI AISE CEFIC American Chemistry The American Cleaning International Association European Chemical Council Centre for Institute for Soaps, Detergents and Industry Council Biocide Chemistries Maintenance Products
EFfCI HCPA MCEC VCI European Federation for Household and Microbial Control German Chemicals Cosmetic Ingredients Commercial Products Executive Council Industry Association Association Driven by science, legislation, regulation and communication, we are working bilaterally, through customer and industry partnerships, to meet our objectives whilst engaging in government and public relations. Our regulatory and advocacy strategy is designed to support innovation by delivering a porolio of new products, integrated solutions and non- chemical alternatives. This enables us to achieve the following: deliver a globally dierentiated customer-focused service that demonstrates the benefits of our products and services; aract and retain the best people with the right competencies, knowledge and talents; ensure our systems and processes, including new digital methods, create a smooth-running and ecient delivery. Arxada’s regulatory advocacy approach Actively managing our chemical substance porolio We prioritize the safety of our employees and customers by manufacturing products that are safe to handle and use. We have implemented robust processes that include monitoring regulatory changes and implementing best practices for the safe use, handling, storage, transportation and disposal of hazardous chemicals. To ensure our commitment to safety, we proactively monitor and track our use of substances classified as category 1 and 2 under the Globally Harmonized System of Classification and Labeling of Chemicals (GHS) for Health and Environmental Hazardous Substances. We have established clear safety protocols for all chemicals used in our operations, regardless of whether they are classified as hazardous. Furthermore, we are dedicated to sustainability and are continuously exploring and implementing safer alternatives to hazardous chemicals in our operations where feasible and appropriate.
Responsible sourcing It is important to us that the materials we use to manufacture our products are procured in a socially and environmentally responsible manner. Sourcing these materials responsibly will allow us to positively impact stakeholders in our supply chain. Ensuring that we have a deep understanding of these issues also helps us identify and mitigate potential risks. We manage our supply chain through our three business units: Consumer Microbial Control (CMC), Industrial Microbial Control (IMC), and Nutrition, Care & Environmental (NCE). Many of the materials we procure are specific to a particular product and site. However, common approaches are used across all business units. We prioritize procuring goods from renewable resources that are grown and produced under environmentally and socially responsible conditions. To ensure our suppliers are aligned with our values and ambitions, we conduct supplier screenings and assessments, and we have updated our global Supplier Code of Conduct in 2022. In addition, we comply with regionally specific requirements, such as the UK Modern Slavery Act Statement, the Swiss Ordinance on Due Diligence and Transparency in relation to Minerals and Metals from Conflict-Aected Areas and Child Labour and the California Transparency in Supply Chains Act Statement. The materials we procure contribute to our greenhouse gas (GHG) emissions footprint that we are aiming to reduce. We can achieve this by selecting more environmentally friendly transportation methods and materials. We also prioritize that workers at our supplier sites are treated safely, ethically and with respect in line with our corporate values of Safety and Health, Ethical Behavior, and Respect for People and Planet. To create more sustainable supply chains across the business, we have set a goal for 100% of our key suppliers to complete an environmental, social and governance (ESG) assessment by 2030. Supplier screening & assessment Prior to entering into a contractual agreement with a supplier, we conduct supplier screening and assessments that consider risk factors such as financial, geopolitical and environmental risk. We are commied to making sustainability improvements within our and our suppliers’ operations. We rolled out our sustainable sourcing strategy in late 2022, designed to comprehensively manage and reduce our Scope 3 emissions by working collaboratively throughout our supply chain. In the future, we plan to join the Together for Sustainability (TfS) initiative and begin ESG assessments of our suppliers using the EcoVadis plaorm. TfS was founded by chemical sector companies in 2011 and aims to support chemical companies in assessing, auditing and improving the sustainability practices of their supply chains. As a TfS member, we will have access to a database of TfS supplier assessments, audits and be able to develop and improve in all areas of our sustainability sourcing practices. TfS audits can be requested by members and are an on-site examination of a supplier’s business sites and practices according to a specific set of sustainability criteria. Audit results are accessible to every TfS member, facilitating in- depth insights into the performance of a supplier.
TfS assessments are conducted online and are supported by EcoVadis questionnaires. Sustainable development experts analyze all supplied data, including third-party certifications and publicly available information, to assign a supplier score from 0 to 100. This score can be broken down by scoring category to identify a supplier’s strengths and weaknesses. As a TfS member, we can request the supplier to put in place a Corrective Action Plan (CAP) to address shortcomings. The CAP includes a roadmap containing corrective actions, deadlines and responsibilities for the supplier to fulfil. To help suppliers implement the roadmap and address identified shortcomings, TfS provides suppliers with access to its academy training hub. By joining TfS, we will be able to make use of the supplier audit and assessment database. We will also be able to calculate an average score across all our suppliers. The initiative also takes considerable burden o our suppliers who need to complete only one assessment to be used by many customers, showing a joint eort across the chemical industry to build more sustainable and responsible supply chains for the sector. As part of our eorts to drive improvements in the supply chain, we will improve sustainability performance through EcoVadis and as a member of TfS, learning from and working with the state of the art sustainability supply chain initiative in our industry. Supplier Code of Conduct In 2022, we refreshed our Supplier Code of Conduct, seing forth our principles for labor, environment, health and safety that we expect all suppliers to observe and comply with. This year, we began the roll out of the code, consisting of nine sections: . Principles . Health and safety . Information . Ethics . Environment . Report to Arxada . Labor . Internal measuring procedures . Termination of agreement The code emphasizes our commitment to following the Principles of the United Nations Global Compact and the International Labour Organization’s (ILO) Forced Labor Standards, the Foreign Corrupt Practices Act, the UK Bribery Act, and all anti-bribery and anti-trust laws of other countries. Through our audits and in the future through our membership in TfS, we will be monitoring our suppliers’ adherence to our Supplier Code of Conduct. If we become aware of a non-compliance with our Supplier Code of Conduct, we have the right to request that our supplier take corrective action and we reserve the right to terminate our agreement with that supplier. Looking forward to 2023 In 2023, we plan to continue the rollout of our sustainable sourcing strategy. This includes having all key suppliers confirm that they are following the principles mentioned in our Supplier Code of Conduct and beginning our engagement with the TfS initiative and ESG supplier assessments, to gain a deeper understanding of our supply chain and help our suppliers progress on their sustainability journey.
HIGHLIGHT Supply chain sustainability helps reduce CO emissions 2 In Visp (Switzerland), one of our biggest sources of CO emissions is our AGU (Acetylene Generator Unit). We have 2 screened the market for renewable and not crude-based AGU-Feedstock and have had several meetings with potential partners. By replacing 1 t of fossil-based AGU Feedstock with renewable AGU Feedstock, we can reduce our fossil-based CO e emissions output by 1 t of CO . 2 2
People We are committed to fostering a diverse and inclusive culture where our employees can thrive and grow. We believe in engaging with our communities and stakeholders to create positive impact. e focus on diversity, inclusion and community engagement is key to achieving our ambitious innovation and sustainability goals. Sandra Collier, Chief People Ocer Our vision for solving the world’s toughest preservation challenges can only be achieved through the hard work and dedication of our people. We want to help our colleagues unlock their talent by providing an inclusive, safe and engaging work environment. Open and respecul communication and engagement with each other, as well as the communities in which we operate, is a fundamental aspect of our business. Empowering every colleague to learn, grow and bring their best skills and abilities to work every day has allowed us to thrive. To continue building a strong business and culture, we have set ourselves three goals. Learn more about how we work to engage our people and communities to create an inclusive and safe culture on the following pages.
Goals Caring for people and our communities, creating safe healthy and inclusive workplaces where everyone can thrive and grow. Towards world-class Creating an inclusive Community health and safety culture where all engagement and throughout our employees thrive and positive impact operations grow through volunteering Achieve by 2030: Increase female Employees share or representation in contribute 46,000 TRIR (Total senior leadership to volunteer hours by Recordable Injury [2] 40% by 2030 2030 Rate) < 0.3 LTIFR (Lost Time Injury Frequency [1] Rate) < 0.1 [1] Rates are calculated as the number of injuries or incidents in the reporting period x 200,000 / Total hours worked in the reporting period. [2] Our senior leadership includes the following job roles: Associate Director; Director; Senior Director; Vice President; Senior Vice President; President; and CEO.
Health & safety Our employees are our greatest asset and we want to ensure we not only respect and nurture them, but keep them safe. Health and safety (H&S) has been defined as one of our three corporate values, and strong H&S processes are essential to maintain our license to operate as a chemical manufacturing business. Our environmental, health and safety (EHS) team oversee our EHS strategy by conducting audits of our operations, addressing remediation issues at our sites and assuring overall compliance. Our EHS eorts are further divided among our business units: Consumer Microbial Control (CMC), Industrial Microbial Control (IMC), and Nutrition, Care and Environmental (NCE). Our CMC and IMC units have a shared EHS approach with their own segment sta, while our NCE segment has a separate EHS team. These teams report into our group operations function and are primarily responsible for managing the day-to-day H&S activities at our sites and facilities. By establishing clear lines of responsibility and oversight at both the corporate and business unit levels, we are eectively managing and promoting a H&S culture throughout our organization, poising us to achieve our global H&S goals. By 2030, we aim to achieve: Below 0.3 Below 0.1 [1] Total Recordable Injury Rate Lost Time Injury Frequency Rate (TRIR) (LTIFR) [1] An injury or illness is considered a recordable incident if it results in any of the following: death, days away from work, restricted work or transfer to another job, medical treatment beyond first aid, or loss of consciousness. Additionally, a significant injury or illness diagnosed by a physician or other licensed healthcare professional is considered a recordable incident, even if it does not result in death, days away from work, restricted work or job transfer, medical treatment beyond first aid, or loss of consciousness. Our health & safety performance At the end of 2021 and into 2022, we launched the Safer Together at Arxada initiative to improve the safety of our operations. The initiative comprises eight themes and focuses on safety culture and reporting discipline. The anticipated result of the increased knowledge and awareness around H&S incidents and reporting was an increase in the number of incidents reported by our facilities. In 2022, we continue to focus on both reporting and managing our TRIR, TRFR and LTIFR. Read more about our Safer Together at Arxada program and our eorts to identify root causes of H&S incidents to prevent reoccurrence below.
Arxada’s 2022 health & safety performance 1.25 Total Recordable Incident 1 Rates (TRIR) Total Recordable Fatality .75 Rates (TRFR) .5 Lost Time Injury Frequency Rate (LTIFR) .25 0 TRIR TRFR LTIFR Safer Together at Arxada As stated above, our Safer Together at Arxada initiative rearms and further integrates the H&S culture at Arxada. Launched by our corporate EHS team, the Safer Together at Arxada program focuses on our values of safety and health, ethical behavior, and respect for people and planet. The program aims to engage all employees to work collaboratively and foster new leadership behaviors in safety; it also acts as a key driver for our 2030 H&S goal. Safer Together at Arxada emphasizes the importance of bringing people together locally and globally, encouraging collaboration and the sharing of learnings and best practices. The program was rolled out globally with the support of our units and all operating regions. It is built around eight themes related to safety management. 1. EHS aspirations and purpose 2. Organizational philosophy and principles 3. Serious injuries and fatalities (SIF) 4. Operating discipline foundations 5. Infrastructure and mechanical integrity 6. Management of change – people 7. Employee engagement 8. Leadership behaviors In 2022, we engaged a wide range of employees in the rollout of our program through various digital and in-person channels, including targeted webinars, workshops, and discussions involving team members at all levels of the business. We also hosted more than 20 seminars on safety leadership behaviors, which were aended by over 200 leaders ranging from senior executives to front-line supervisors. In November 2022, we conducted a survey that showed 80% of all our employees were already familiar with the program and 68% were already seeing a positive impact. Additionally, our survey showed that 92% of all employees see themselves commied to the new EHS aspiration and purpose statement that was developed and communicated by a global team as part of this roll out eort.
Arxadawilladvance the safetyofevery employee, every task, every day,and protect the environment wetouch. As part of eorts to implement Safer Together across Arxada, we also revised and updated 21 internal safety-related policies and procedures to ensure strong support for our new purpose of using beer science to solve the world’s toughest preservation challenges. In 2023, we will continue rolling out the program across our global operations, focusing on oce-based employees. Creating a health & safety culture Our strategy aims to embed an awareness of H&S measures in our corporate culture. We want our employees to understand the importance of H&S and live our safety and health value in their everyday actions to ensure they are kept safe. To enable this, each employee has an annual performance goal related to H&S. Together with the employee’s manager, this goal is tailored to take into consideration the employee’s job responsibilities, working environment, and their contribution to Arxada’s broader regional and global H&S goals. In addition to the annual performance goal, every employee completes H&S related training on an annual basis. All our employees are required to complete basic H&S training, including all relevant standard operating procedures for the processes performed by the individual. For example, some oce-based and sales employees may be required to receive training on topics such as our policy on using phones when driving, while those who work with chemicals receive training on the safe and lawful handling of chemicals. Additionally, some employees complete theoretical and practical exams over longer time intervals. By providing tailored training to our employees, we are ensuring that they are equipped with the knowledge and skills needed to work safely and eectively in their roles. Employees also regularly participate in emergency response drills specific to each site. Management & auditing of sites The corporate group EHS team is responsible for regularly auditing all our sites, ensuring that site-level EHS practices comply with regional laws and our own policies. This also allows us to mitigate EHS-related risks and implement measures to standardize practices globally. In addition to following regulatory auditing requirements, we follow a risk-based auditing system, grouping our sites into risk categories that determine the frequency of their auditing. At a minimum, every site is audited every three years. Depending on the outcome of an audit, a site may be classified as higher-risk and be audited more frequently. During audits, we assess our sites based on their risk management systems and performance (S&P), and compliance with a range of EHS-related issues, including H&S measures, emergency preparedness and response, and the handling, storage, and disposal of waste. In the US, for example, our sites must ensure compliance with Occupational Safety and Health Administration (OSHA) standards. In addition to these broader topics, we also conduct assessments for industrial hygiene and personal protective equipment to ensure the safety of our employees. When new facilities become part of Arxada, we conduct a separate EHS gap assessment in addition to our regular auditing process. This assessment is designed to identify areas where current practices may need to be improved or established to meet our standards. Aer completing the assessment, our EHS teams work with the evaluated sites to discuss the findings and develop an action roadmap for the next 12 to 18 months to address any identified weaknesses. By proactively identifying and addressing potential EHS issues, we are ensuring that all our sites operate in a safe, compliant, and sustainable manner. In 2022, we carried out 19 audits and assessments across the 28 sites included in our global audit program.
Arxada site audits 2022 x5 x8 x6 Risk management Environmental, EHS gap plans and process health and safety assessments safety management S&P audits audits Events & incidents While we are working hard to maintain a rigorous and comprehensive H&S culture in our business and at all our sites, incidents can happen. When an incident does occur, we learn from it and put measures in place to prevent it from reoccurring through two specific approaches: . Root cause analysis: Using the definitions of the Center for Chemical Process Safety (CCPS) for leading and [1] [2] lagging process safety metrics, we request a root cause analysis for every registered Tier 1 and 2 incident. Using root cause analysis, we can understand why an accident occurred and implement measures to prevent it from occurring again. In 2022, we have been working to align this methodology across all our global operations. To broaden the reach and eectiveness of our root cause analysis, the analysis itself, including the cause mapping, is shared with all EHS and site managers during a global monthly call. This allows us to implement our learnings from one incident on a global scale. . Serious Injuries and Fatalities (SIF) program: As part of our Safer Together at Arxada program, we implemented a SIF program and integrated this into our corporate H&S processes. As part of this, SIF training was carried out at manufacturing sites globally, and we are commied to thoroughly investigating all registered incidents and examining their potential to cause acute injury or fatalities. By actively engaging our employees and managers in this process, we aim to identify and eliminate any potential sources of serious harm at our operations. [1] Leading metrics are a forward-looking set of metrics that indicate the performance of the key work processes, operating discipline, or protection layers that help prevent potential incidents. Lagging metrics are a retrospective set of metrics based on incidents that meet an established threshold of severity. [2] Tier 1 incidents are described as catastrophic and exceed a defined threshold level, whereas a Tier 2 incident is used to normalize the industry metrics and provide a minimum and upper limit threshold range. Looking forward to 2023 In addition to continuing the roll-out of our Safer Together at Arxada program and auditing new and existing sites in 2023, we plan to integrate wellbeing and mental health more formally into our overall H&S approach. This will be intricately connected to our employee engagement and community involvement eorts. By addressing both physical and mental health, we will create a comprehensive approach to H&S that promotes the overall wellbeing of our workforce.
HIGHLIGHT Promoting a strong safety culture at Lake Charles, USA Our Lake Charles facility in Westlake (LA, USA), is a flagship example of Arxada’s H&S culture. The site produces hydrazine products for our Nutrition, Care and Environmental business segment and has been recognized for its outstanding H&S performance. Over the last 26 years, there has been no Lost Time Injury incident at the site and the previous OSHA recordable injury occurred in early 2011, demonstrating an exceptional safety record. This is especially important to us as hydrazine needs to be handled with care to avoid negative health consequences. The team at Lake Charles understands the importance of handling hydrazine carefully and fostering a safety culture of looking aer each other. Employees at the site regularly review and adapt their own and their colleagues’ work procedures to make processes safer. New hires at Lake Charles complete intensive training focused on H&S to ensure a good understanding of the safety procedures and risks associated with handling hydrazine and other materials.
Aracting, enabling & engaging a diverse workforce With a rich legacy more than a century strong, our shared passion and purpose motivates us to innovate and find solutions to the world’s toughest preservation challenges. We believe that aracting, enabling and engaging a diverse workforce is crucial to our success. By fostering an inclusive culture and hiring team members from a range of backgrounds and experiences, we are beer able to tackle the complex and varied challenges facing the world today. Aracting & developing talent As a young and dynamic business operating in a competitive industry, it is essential to prioritize the araction and retention of top talent. By creating a unique and distinct business culture led by recognized leaders in the chemicals industry, we can oer our employees the opportunity to shape and grow with the company. This makes us an aractive employer for new hires and emphasizes the importance of engaging with and developing our current team members. By valuing our workforce and providing meaningful work, we are building a strong and sustainable business. For our new hires and established workforce, we have both employee training and individual employee development plans. On an annual basis, all sta is required to complete compliance training that includes instruction on our Code of Conduct. Additionally, all employees have access to LinkedIn Learning to develop specific skills based on their jobs and interests. Our talent araction eorts in 2022 were primarily led by individual sites and regions. This included regional partnerships with organizations focusing on women in science, technology, engineering and math (STEM) and early careers apprenticeship programs. In 2023, we will focus on ensuring that our talent araction processes are designed to include diverse slate hiring pools and target specific communities in line with our goal to build a workforce that is more diverse in gender, race, background and skillsets. Diversity, equity & inclusion Having a more diverse, equitable and inclusive workforce is a critical component of our global employee strategy. Diversity is important for beer decision-making, higher quality ideas and innovation. We are commied to creating a workplace where all employees can bring their full selves to work every day, participate authentically and are valued for their unique talents and perspectives.
As a global company with a global customer base, we understand that diversity looks dierent in every part of the world, and we want our business to be reflective of all the markets in which we operate. We recognize that the chemicals industry has historically had a skewed gender ratio, and we are commied to playing a role in promoting greater diversity within the industry. One way we are working towards this goal is by seing a target for our leadership team to achieve 40% female representation by 2030. This year, female representation in our senior leadership team [1] was 23%. To demonstrate our commitment to diversity, equity and inclusion (DEI) at the leadership level, in 2022 we began actively communicating our diversity statistics and measures to our Executive Leadership Team (ELT). While DEI is sponsored at the executive level by our Chief People Ocer, Sandra Collier, our CEO Marc Doyle is actively involved in and passionate about driving forward awareness and progress of this important work. Equally, DEI is being championed at the operational level by a group of passionate employees who established a DEI steering commiee in 2022, aiming to foster a diverse, equitable and inclusive culture at Arxada. To aract top talent, we are developing a talent engine roadmap with specific workstreams focused on aligning job levels and performance measures globally, standardizing our approach to early careers, and creating a plan for employee learning and development that includes training for line managers. Our talent engine roadmap will link to our DEI ambitions, creating a more diverse talent pipeline. This will include targeted partnerships and job descriptions containing gender-neutral and inclusive language. By implementing these strategies, we strengthen our position as an aractive and supportive employer for top talent. While DEI representation and commitment at the leadership level is important, we are working on creating a more diverse talent pipeline for all career levels by ingraining DEI into our talent araction processes. Arxada workforce diversity 2022 [1] [2] Arxada senior leadership Arxada global workforce Female Female (23%) (25%) Male (77%) Male (75%) [1] This data excludes senior leadership from our recent Troy and Enviro Tech transactions. Our senior leadership includes the following job roles: Associate Director; Director; Senior Director; Vice President; Senior Vice President; President; and CEO. [2] Please note the data provided is only for Arxada (legacy LSI), which represents 74% of the company. Engaging employees Employee engagement is the key to retention, and our fast-evolving business makes it important to listen to our employees while providing them with a strong understanding of our purpose and values. To do so, we are providing our employees with regional guidance and are engaging them through awards and a specialized engagement survey.
All employees have access to an employee handbook that contains guidelines on policies and practices that are specifically applicable to their region. The handbook helps employees beer understand their job expectations, as well as Arxada and the company culture. It contains practical information on employee benefits, and outlines how misconduct, such as harassment and discrimination, is handled. Our employee handbooks reflect our company values and reinforces our Code of Conduct. Learn more about our Code of Conduct, values and approach to business ethics. To ensure we are eectively promoting areas such as diversity and inclusion, and health and wellbeing within our organization, we value and rely on feedback from our employees. To gather this feedback, we use Peakon, the employee engagement plaorm for our Insights2Action survey. This initiative is deployed across our organization to measure our drivers of employee engagement including role rewards, recognition, workload and other items that contribute to an overall engagement score. We work with local teams to develop and agree on action plans to improve their scores and engage employees more eectively. The survey also provides an employee Net Promoter Score (eNPS). The eNPS tells us how likely our employees are to recommend Arxada as a place to work to family and friends, thus providing an additional measure of employee engagement and satisfaction. In 2022, our eNPS was 7.2 and we aim to achieve a score of 7.5 by 2024. We will work to improve our engagement with eNPS by providing enhanced training for line managers to enable them to have more meaningful development conversations and oer beer support for their teams. Insight2Action survey results are shared at the individual team level. Both the team results, as well as global results, help us identify areas across the business that need more support and aention in 2023. Arxada’s 2022 Insight2Action scores 73% 7.2 Of our employees responded to our Our 2022 eNPS score employee survey in 2022 Looking forward to 2023 In 2023, we will expand and grow our DEI eorts. The DEI steering team will work to build a more comprehensive strategy to drive progress toward our goals and build a foundation for nurturing a culture of inclusion and belonging. Our DEI eorts will be further supported by the launch of our employee resource groups (ERGs). Through our ERGs, we will aim to hear the authentic voices of our employees and understand their motivations and needs. This input will help us build the supporting policies, frameworks and practices required to reach our targets and goals, and create a true culture of belonging. We aspire to maintain this continuous feedback loop to ensure our employees feel heard and included.
HIGHLIGHT Izzy Colon technology & innovation award This year, we launched the Izzy Colon technology and innovation award to engage and incentivize our employees to continue innovating and developing high-quality products. This award is named in honor of Izzy Colon, a respected leader and industry icon in research and development, innovation, new product technology and technical services who retired in 2022. Izzy, who is part of the award commiee, believes that innovation needs to: Provide a sustainable competitive advantage Solve an important problem that the company is facing Show real creativity By recognizing the importance of innovation through this award, we aim to keep Izzy’s legacy alive and encourage our workforce to continue pushing the boundaries of what is possible. By engaging our employees in product innovation and valuing their contributions, we are fostering a culture of innovation that helps to drive the success of our business. We look forward to announcing our first award winners in early 2023.
Community involvement Engaging with the communities around the sites where we operate allows us to communicate with, learn from, and contribute to our local communities, building positive relationships and having meaningful impact. Our sustainability strategy solidifies our global commitment to create positive impact in our communities. By providing our team members with the opportunity to give back to their communities, we hope to foster a sense of purpose and connection amongst our employees. In 2022, our sites largely organized their own community engagement eorts. For example, our employees in Alpharea (GA, USA) donated time for important community initiatives including the Urban Tree Planting Plan in downtown Atlanta (GA, USA). In Huddersfield (UK), employees coordinated a community food drive in support of local food banks. In Salto (Brazil), we partnered with local schools and municipalities to develop a tree preservation program. The goal of this individualized approach is for each program to personally connect with our employees in a meaningful way, while upliing the communities where we live and operate. To increase our engagement and impact, our goal is to share 46,000 hours of paid volunteer time by 2030. The hours correspond to a day of volunteering every year for 20% of our current employee census. We expect this activity to expand over time as sites and employees detect needs, find ways to contribute and time allotment is increased. The communications department will steer the eorts to build a robust community engagement policy and multiyear plan in 2023, in collaboration with the EHS team and our sites. It will rely on local employee resource groups to start implementing activities that maer to Arxada and to our communities. Looking forward to 2023 In 2023, we will enhance these eorts as we launch our engagement and volunteering program. The program will empower employees to make a meaningful impact through hands on community involvement by volunteering with organizations in our respective communities where we live and work. The intent is to create and facilitate opportunities to have a meaningful influence in our communities locally, while aligning and supporting our purpose, values and strategy globally.
HIGHLIGHT Downtown Atlanta urban tree planting – One Million Trees initiative In 2020, the One Million Trees Initiative — a collaboration of ten metro Atlanta cities and ten local non-profits was launched to plant and conserve 1,000,000 trees in ten years. The initiative is seeking to address local climate eects and environmental stresses from urban growth, as well as improve the cities’ sustainability and beer protect the health and wellbeing of people living and working in metro Atlanta (GA, USA). As part of our corporate volunteering work, employees from three of our Atlanta based wood sites volunteered with the local non-profit Trees Atlanta which is part of the initiative. Our employees from the Conley Plant, Conley Technical Center and Alpharea R&D site volunteered to plant trees at South Bend Park located close to the Conley facility in February 2022. Their eorts with Trees Atlanta contributed to the wider One Million Trees Initiative and the sites are looking forward to continue volunteering with Trees Atlanta and the One Million Trees Initiative on a regular basis.
Resources & downloads 2022 Sustainability Report Assurance of Environmental Data 2022 Sustainability Report (PDF) Independent Limited Assurance Statement to Arxada AG Arxada Certificates 2022 Sustainability Report Data Indices Policies Planet Pillar Data Code of Conduct Preservation Pillar Data Supplier Code of Conduct People Pillar Data Arxada Sustainability Policy Complete Sustainability Report Data Arxada UK Modern Slavery Statement Act 2022 Arxada California Transparency in Supply Chains Act Statement
Data index Notes on data completeness Financial Year 2022 is Arxada’s inaugural year of ESG reporting. Due to this, some data in the report is incomplete. We are commied to increasing the scope of our sustainability data collection and data assurance in future years. General disclosures Performance indicator FY22 Framework Organization name Herens Midco S.a.r.l. GRI 21 Ownership status Private equity, owned by Bain and Cinven funds, holding GRI 21 company Headquarters location Basel, Switzerland GRI 21 Countries of operation See Our business & sustainability GRI 21 Entities in sustainability reporting Troy AG and Arxada AG GRI 22 Dierences between entity list in N/A Audited Financials on Herens Midco S.a.r.l. are non- GRI 22 financial reporting and public information sustainability reporting Reporting period (sustainability 01.01.2022 – 31.12.2022 GRI 23 and financial reporting) Report cycle Annual GRI 23 Report publication date 23.05.2023 GRI 23 Report contact point General inquiries on sustainability report: GRI 23 [email protected] Investor inquiries: [email protected] Restatement of information N/A inaugural report GRI 24 External assurance External assurance was sought for the assessment of GRI 25 embedded KPIs in our Sustainability-Linked Financial Instruments, covering Scope 1 and Scope 2 (location- based and market-based) as well as total waste generated for our Sustainability Report for the reporting year 2022. See Our 2022 Assurance Leer from ERM-CVS and Our business & sustainability Sector Chemicals sector GRI 26 Value chain and activities See About Arxada GRI 26
Performance indicator FY22 Framework Governance structure and See Our Executive Leadership Team and Sustainability GRI 29 composition governance Nomination and selection of the See Sustainability governance GRI 210 highest governance body Chair of the highest governance Arxada does not have a formal Chairman of the Board GRI 211 body Role of the highest governance See Sustainability governance GRI 212 body in overseeing the management of impacts Remuneration policies See Sustainability governance GRI 219 Statement on sustainable See Sustainability at Arxada and Our business & GRI 222 development strategy sustainability Policy commitments See Sustainability governance and Resources & GRI 223 downloads Arxada’s policies are approved by the relevant ELT members and boards of the relevant legal entities. The policies mentioned above are communicated through the Arxada internet, intranet, and periodic ethics & compliance training programs, such as its True Oce training plaorm, and periodic Legal Department training programs. Embedding policy commitments See Sustainability governance and Aracting, enabling & GRI 224 engaging a diverse workforce Processes to remediate negative See Our business & sustainability GRI 225 impacts Several of the company’s manufacturing sites, including Visp, Newark, Mapleton, Willamsport, Conley and Suzhou, have labor unions, which have Collective Bargaining Agreements (CBAs) under relevant local laws containing grievance mechanisms. In the event the company receives claims or complaints from employees or third parties, the Legal Department thoroughly investigates them with the appropriate internal stakeholders and business/functional partners, supported by outside counsel where necessary, and works with internal stakeholders to determine appropriate actions. Processes involving the Legal Department are periodically reviewed and evaluated as needed, depending on a variety of factors. Mechanisms for seeking advice The HR and Legal Departments typically support GRI 226 and raising concerns grievance processes. Guidance regarding reporting concerns is included in several company policies (such as some mentioned above), during training programs and during everyday business counselling.
Performance indicator FY22 Framework Approach to stakeholder See Our business & sustainability and Advocacy GRI 229 engagement leadership for science-based decision-making for a sustainable future Planet pillar disclosures Performance indicator FY21 FY22 Framework [1] [2] Greenhouse gas emissions Scope 1* 658,222 tCOe 181,138 tCO e GRI 3051, 3052, 2 2 3055 Scope 2 location-based* 173,871 tCO e 155,514 tCO e 2 2 Scope 2 market-based* 168,216 tCO e 163,052 tCOe 2 2 Base year 2021 Consolidation approach Operational control Operational control Standards, methodologies, GHG Emissions are defined GHG Emissions are defined assumptions, and/or calculation as Scope 1 and 2 as Scope 1 and 2 tools greenhouse gas emissions greenhouse gas emissions of the Group, determined in of the Group, determined in accordance with the Scope accordance with the Scope 1 and 2 guidance of the 1 and 2 guidance of the GHG Protocol Corporate GHG Protocol Corporate Accounting and Reporting Accounting and Reporting Standard. Standard. [1] Air quality management NO 75.0 t 68.6 t SASB RT-CH-120a.1 X SO 3.8 t 3.8 t X VOCs 166.3 t 168.8 t [1] Energy management Total energy consumed 5,616,650 GJ 5,043,030 GJ SASB RT-CH-130a.1 % grid electricity 30% 32% % renewable 5% 1% Waste management Third-party waste management See Supplier Code of See Supplier Code of GRI 3062, 3063, Conduct. Additionally, Conduct. Additionally, 3064, 3065 legislative compliance is legislative compliance is administrated locally based administrated locally based on local legislation. on local legislation.
Performance indicator FY21 FY22 Framework Total waste generated* 70,717 t 53,881 t Hazardous waste generated 57,670 t 41,203 t Non-hazardous waste generated 13,047 t 12,678 t Hazardous waste recycled 6,899 t 5,109 t Non-hazardous waste recycled 2,522 t 2,585 t Hazardous waste incinerated 34,671 t 31,583 t Hazardous waste sent to landfill 3,034 t 1,240 t Hazardous waste disposed (other 13,064 t 3,269 t options) Non-hazardous waste 1,573 t 2,483 t incinerated Non-hazardous waste sent to 8,951 t 7,610 t landfill Location of disposal 100% of waste captured is 100% of waste captured is directed to osite disposal. directed to osite disposal. [1] The scope of this report includes all manufacturing sites with FTE >10 (note, Auckland New Zealand and Trentham Australia manufacturing sites are included even though they have less than 10 FTEs) and Pilot Manufacturing sites with FTE >45. The scope excludes emissions and waste from oces, as emissions and waste from these locations are not material to Arxada’s overall emissions and waste. [2] Our Scope 1 includes fuels (i.e. LPG, Fuel Oil, etc.) direct emission to air from our operations including CO , N O, CH . Arxada does not have emissions from PCF, HFCs and SF . Our Scope 2 emissions are market-based and composed 2 2 4 6 of purchased electricity and steam. * Metrics have been assured by ERM CVS. For more information, please see the “External Assurance Statement” which details the scope, activities and conclusion of their engagement. Preservation pillar disclosures Performance indicator FY22 Framework Safety & environmental stewardship for chemicals % of products containing GHS 77% SASB RT-CH-410b.1, category 1 and 2 health and RT-CH-410b.2 environmental hazardous substances % of products containing GHS 100% category 1 and 2 health and environmental hazardous substances with a hazard assessment Management of the legal & See Advocacy leadership for science-based decision- SASB RT-CH-530a.1 regulatory environment making for a sustainable future Child labor and forced or See Supplier Code of Conduct GRI 4081, 4091 compulsory labour
[1] People pillar disclosures Performance indicator FY22 Framework Workforce health & safety Total Recordable Incident Rate 1.21 SASB RT-CH-320a.1, (TRIR) RT-CH-320a.2 Total Recordable Fatality Rate 0 (TRFR) Lost Time Injury Frequency Rate 0.41 (LTIFR) Operational safety, emergency preparedness & response Process Safety Incidents Count 38 SASB RT-CH-540a.1, (PSIC) RT-CH-540a.2 Process Safety Total Incident .98 Rate (PSTIR) Number of transport incidents 0 Diversity & equal opportunity Senior leadership gender GRI 4051 Male 158 77% diversity Female 46 23% Gender diversity Female 934 25% Male 2,866 75% Not declared 0.15% Non-discrimination See our Code of Conduct GRI 4061 Employment Total employees 3,600 GRI 4011, 4012, 4013 New hire gender diversity 157 Hires in 2022 Female 23% Male 53% Not declared 24% Turnover gender diversity The total turnover rate for 2022 is 17.25%. We are unable to provide a turnover rate by gender for 2022. Full-time employee benefits For US FTEs: Medical Dental Vision
Performance indicator FY22 Framework Life Insurance Disability Coverage 401k participation Significant locations of operation See Our business & sustainability Parental leave entitlement female variable by region and location Parental leave entitlement male variable by region and location Parental leave female 1 (based on last 6 months of 2022 only) Parental leave male 1 (based on last 6 months of 2022 only) Community relations See Community involvement SASB RT-CH-210a.1 Training & education See Aracting, enabling & engaging a diverse GRI 4042 workforce and Health & safety [1] People pillar data is only available for 2022. Please also note that the data provided is only for Arxada (legacy LSI), which represents 74% of the company. The total headcount for 2022 includes 100% of the workforce for 2022, including legacy Arxada, TROY and Envirotech.